自乳化药物传递系统处方设计的计算机模拟研究
摘 要:从热力学和动力学角度对自乳化系统进行了计算机模拟研究,计算机模拟是研究自乳化系统结构和特性的方法,并对它的应用前景作了进一步的展望。利用Material Studio 4.2中的耗散粒子动力学(DPD)方法对可用于自乳化药物在水中的聚集体形态进行了模拟。模拟结果表明:比例对表面活性剂聚集体影响较大。随着表面活性剂浓度的增加,聚集体由球形向棒状转变;
关键词:耗散粒子动力学(DPD);表面活性剂;比例;形态;模拟
前言
自乳化技术被广泛用于农药和杀虫剂工业已有多年。自乳化药物传递系统(Self—Emulsifying Drug Delivery System,SEDDS)是由油相、非离子表面活性剂和助表面活性剂组成的固体或液体制剂,其基本特征是可在胃肠道内或环境温度适宜(通常指体温37摄氏度)及温和搅拌的情况下,自发乳化形成的。而当亲水性表面活性剂(HLB>12)含量较高或同时使用助乳化剂时,在轻微搅动下可制得更精细的乳剂(粒径<100 am),则被称为自微乳化药物传递系统。目前已有先进的实验方法用于分析自微乳化药物传递系统如静态和动态的光散射,小角X光散射,小角中子散射等散射技术及傅里叶变换红外,紫外,核核磁共振等光谱技术。除X射线可得到直接结构信息外,其它实验方法不能提供自乳化药物传递系统的微观结构和动态性质。因此人们用计算机模拟研究自乳化药物传递系统,力求提供微观结构和性质。研究自乳化过程模拟,可以更深入地了解表面活性剂各种作用的微观机理为其应用提供理论指导。Material Studio 4.2中的耗散粒子动力学(DPD)模块是Accelrys公司的一个计算机模拟程序。这种方法可以从分子水平上研究介于微观和宏观之间的一些性质,可以通过DPD方法模拟表面活性剂在溶液中的介观相
[5-8]。DPD模块通过理论模拟,从介观水平上为实验提供参照,有利于新型表面活性剂的研制和开发,从而可节约成本,缩短研发时间。
1. 模拟与方法
1.1模拟原理
表面活性剂分子含有两个或两个以上的疏水尾链、亲水头基和一个连接基团,因此DPD模型中定义疏水尾链、亲水头基两种粒子。粒子与粒子之间彼此采用简单的谐振动弹簧连接,每个粒子代表表面活性剂分子中相应大小和长度的基团
[10,11,13],所用粒子连接在一起形成表面活性剂分子的DPD模型。在模拟中建立了Flory Huggins参数
x与DPD参数α
ij之间的线性关系
[8,14],进而把Flory Huggins参数转化为模拟中的DPD相互作用参数。当
x>0,即α
ij>25时,粒子之间倾向于相分离;α
ij<25时,粒子之间倾向于相互吸引(混合);而认为当α
ij=25时,粒子之间无作用
[7]。选取不同的参数表示表面活性剂的头基、尾基、联接基和水相互作用的不同,则可用此相互作用参数描述表面活性剂和水彼此间相互作用的大小。运用单一变量的原理设置表面活性剂,水,油相互作用的DPD参数。计算的参数列于上表中。X=V
ref(δ
i-δ
j)
2/RT在20×20×20大小的立方格子中进行模拟,粒子的密度为ρ=3.0,因此,模拟体系中包含3000个粒子
[8,9](包含水粒子和表面活性剂粒子),10000步的模拟,**终得到模拟平衡状态。通过不断地向模拟格子中添加表面活性剂分子,以研究浓度变化对表面活性剂聚集形态的影响。模拟开始时,所有体系均采用随机分布,在各个方向应用周期性边界条件,通过一定步数模拟,**终得到模拟达到平衡的表面活性剂分子的聚集形态。
1.2模拟条件设置
(1) 分子模型设置:表面活性剂(Diblock):A 1 B 4 水(Water):W 1 油(Oil):O 1
(2) 模拟体系大小:20×20×20
rc3
(3) 相互作用力(Interactions)设置如下表
表1 本课题粒子的DPD相互作用参数(DPD单位)
|
A |
B |
W |
O |
A
B
W
O |
25
90
28
80 |
90
25
70
29 |
28
70
25
100 |
80
29
100
25 |
(4) 时间步长(time step)设定为0.05,每1000个时间单元重新开始构型。每10000个步长重新在前一个结果下继续计算(Restart),并自动保留结果。
(5) 相对含量(Relative amount)
表2 本课题粒子的相对含量
|
Fraction |
1 |
2 |
3 |
Diblock
Water
Oil |
0.01
0.98
0.01 |
0.05
0.90
0.05 |
0.10
0.80
0.10 |
#p#分页标题#e#
2 结果与讨论
2.1表观分析
表面活性剂的浓度(摩尔分数为单位)对聚集体的形态有显著的影响。下图1,2,3依次为相对含量图表中的第1,2,3组实验数据所得。由图可见,表面活性剂浓度的增大有利于表面活性剂在水中形成胶束聚集体。随着表面活性剂浓度的增加,聚集体由球形向棒状转变,趋势与文献报道的一致
[10,11]。
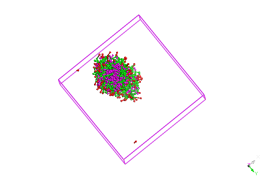
图1表面活性剂浓度为1%时的聚集形态
增加表面活性剂浓度,表面活性剂更易发生由不规则形状的胶束向球状胶束的转变。表面张力,聚集度对聚集体的影响是主要因素。随着表面活性剂的增多,聚集数增加,表面活性剂所包的油分子聚集体从不规则形状逐步向表面张力更小,聚集度更大的球状聚集体转变。当表面活性剂浓度即胶团聚集数足够大时,聚集体形状就转变为棒状
[10]。
图2表面活性剂浓度为5%时的聚集形态
图3 表面活性剂浓度为10%时的聚集形态
因此,表面活性剂更易形成聚集数大的聚集体,其形态容易发生由不规则形状到球形再到棒状的转变。
2.2内部剖面分析
以上看到的都是外部形貌,为了更清楚直接地了解自乳化微粒的内部结构,我们作了进一步的分析。如下面图4,是图2表面活性剂浓度为5%时的聚集形态的内部剖面图。可以很清楚的看到表面活性剂和水、混合体系的内部分子分布情况:
图4表面活性剂浓度为5%时的聚集形态的内部剖面图
图4中内部为表面活性剂的疏水端紧密聚集包围油分子成球状结构,外部为表面活性剂的亲水端均匀分布在球的外侧形成一层膜状结构,两者作用使体系更加稳定。随着表面活性剂浓度的增加内部亲油端排列更为紧凑,外部亲水端分布更加致密,逐渐形成棒状结构,从而使整个体系更加稳定的。
各组分间的混合比例是控制胶束形貌的关键因素之一。无论从表观形态还是内部剖视我们都可以发现:通过小幅度改变各组分混合比例,混合体系中的各组分便会形成一系列具有全新形貌和内部结构的聚集体。
4 结 论
利用DPD模型模拟了不同结构表面活性剂在水中的聚集体形态。随着表面活性剂浓度的增加,聚集体由球形向棒状转变;
对于表面活性剂、油、水混合体系来说,三种组分间的混合比例是控制胶束形貌的关键因素之一。仅仅通过混合比例的小幅度改变,混合体系便自组装形成一系列具有全新形貌和内部结构的聚集体。
当然,上述结论还只是定性的。本文所研究的体系及采取的研究手段,是一种较为前沿的方法,对体系的复杂性还有待于更充分的认识,对不同分子的类型还需要采取更多的研究手段,全面描述分子在水溶液中形成胶束的机理还需要深入的研究。尽管如此,本文的工作为胶束的应用展示了良好而广阔的前景,为下一步的深入研究打下了良好的基础。